2023.12.14
“作業時間の見える化”で生産効率と人手不足の改善へ!
株式会社サンテック「製造業」
株式会社サンテック(以下、同社)は、半導体用シリコンウエハのダイシング・研削加工を提供する会社で「ダイシング加工」ではパイオニア的存在として知られている。「ダイシング加工」とは、平面材料を縦横・サイの目に切断して小さなチップやダイスにする加工をいう。切断する素材は薄いシリコンウエハからサファイアなどの硬い鉱石まで多種多様で、素材によって切断するブレード(刃)の種類や回転数などを適切に選択する。さまざまな顧客のニーズに応えられるのは、同社の高い技術力と長年培ってきた経験によるものである。
「メーカーの開発部門、大学の研究室などから相談を受けることも増えています」と話してくれたのは代表取締役社長 日野広美氏。毎月100件を超える多種多様な素材の加工を行う同社では、多くの要望に応えるためには業務効率の向上が必要と感じ、デジタル化への取り組みを始めたという。
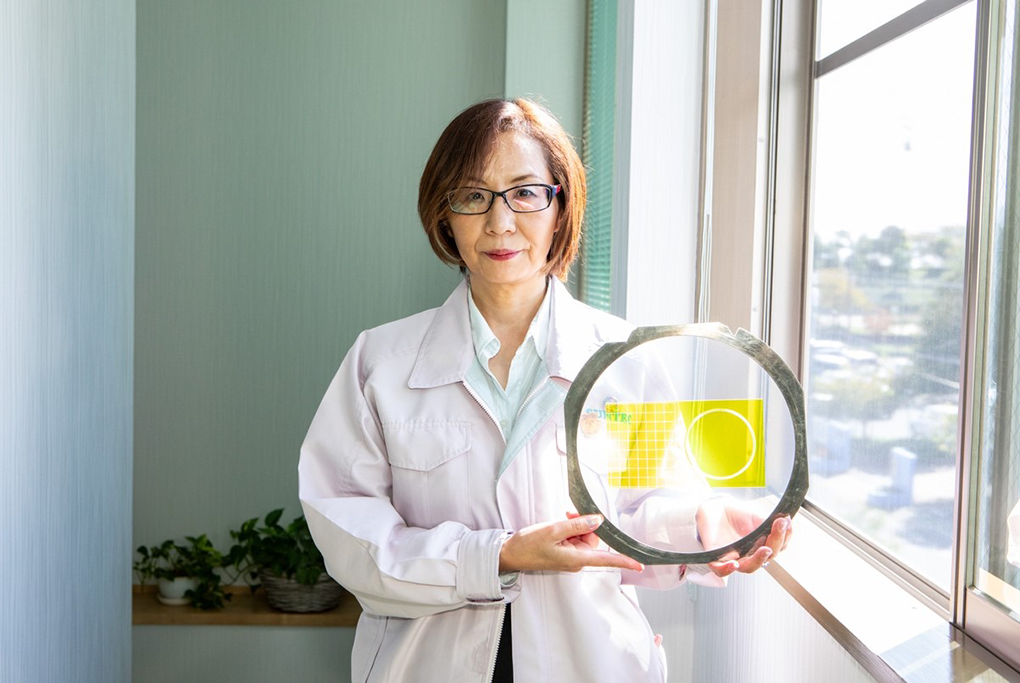
“ペーパーレス化”に挑戦!
~紙ベースの進捗管理からIoTセンサーシステムへ
現場では“紙での手書き”を中心としたアナログな手法で工程の進捗管理が行われていた。ダイシング・研削などの加工を行う機械を使用する際、品名・相手先などの基本情報・作業員の氏名・作業開始から終了までの時間などを記録用紙に記入し、その記録用紙をファイリングして工程状況の把握を行っていた。日野氏は「手書きは書く手間と記入漏れや書き間違いもありましたから、とにかく“紙への手書き”をなくしたかった」と言う。
同社は以前から付き合いのあった東京都中小企業振興公社(以下、公社)担当者の勧めで、デジタル技術活用推進事業(以下、当事業)を利用した。当事業により派遣された専門家からのペーパーレス化の提案の中から、現場の作業員に負荷がかからないIoTセンサーシステムの採用を決意した。 今回、導入したIoTセンサーシステムではすべての加工機にセンサーを取り付け、作業員は自分に付与されたバーコードをセンサーに読み取らせてから作業に着手し、作業を終えたら再びバーコードを読み取らせる。これらの記録はすべてコンピュータに蓄積され、社内のパソコンで加工作業の記録を閲覧できるようにした。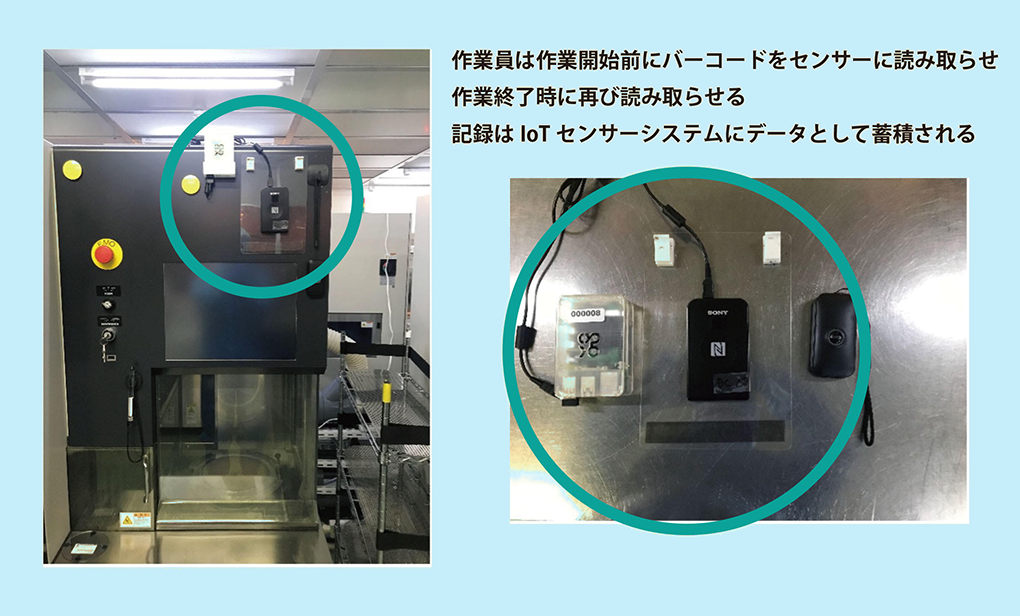
的確な”時間管理”で営業のスケジュール精度が向上!
~見えていない作業時間が“見える化”
記録用紙に記入せず用紙をファイリングしない“ペーパーレス化”を成し遂げることで、現場作業の効率の向上に繋がったがそれ以外にも大きなメリットがあった。それは“作業時間の見える化”だ。
新規の取引先から声がかかることが多い同社では、営業が新規取引先に提出する加工スケジュールをこれまでの経験と現場の声からおおよその作業時間を算出していた。しかし、今回のIoTセンサーシステム導入で過去に行った作業時間の記録を取り出し、類似する前例の照合が容易となった。おかげで、より具体的かつ精度の高いスケジュールを出せるようになったという。 「過去に似たような案件を何時間でやったのかを参考にできますし、作業員ごとのスキルも見えるようになって、現場での作業員の配置も含めたスケジュールを考えられるようになりました。まだ導入して間もないですが作業時間管理においても大きなメリットがあると思います」(日野氏)専門家の協力で納得のいくシステムを実現!
~自社ニーズに合致したプログラム導入
これまで記録用紙への記入と、用紙のファイリングを行う膨大な記録ファイリングから過去の作業履歴を探すといった「見えていない作業時間」が発生していた。これからは見えていない作業時間を他の作業に充てることが可能となったことで、同社では人手不足の解消や時間短縮などにも期待を寄せている。
導入したIoTセンサーシステムのプログラムは、パッケージ製品ではなく、システム会社に依頼してゼロから開発した。「パッケージ製品では購入した時点で終わり、私たちが“こうして欲しい”という機能があっても、私たちがプログラムに合わせなければいけません」と日野氏は言う。今回のIoTセンサーシステムのプログラムは、システム会社と話し合い、年間で検証を重ねながら納得のいくシステムを追求していった。 「導入に対して社員が興味をもってくれて、システムについて多くの意見を出してくれました。本当に社員が使いやすいシステムでなければ導入しても、使われなくなってしまうと思います。パッケージ製品の良さもありますが、自分たちが使いやすく継続して使えるシステムを目指しました」(日野氏) 日野氏は、このシステム会社と交渉を行う上で、公社から派遣された専門家がさまざまな役割を担い大きな存在感を示したと言う。システム会社の紹介から技術解説まで、交渉の交通整理のような役割を担ったのが専門家だった。同社は専門家と意見交換を行いながら納得のいくシステムに仕上げていくことができた。 同社では、以前から業務へのデジタル技術の導入を進めており、すでに2つの取組を行っていた。 ①営業情報を共有するシステム②現場が受注一覧を確認できるシステム 今回のIoTセンサーシステムは3つ目の導入となることから、デジタルツールの導入に社員も理解を示し、積極的に活用している。 「まだまだデジタル化したい部分はあって、本当なら一気に実行したいところですが、予算があってのことなので計画的に進めていきます。これからも公社の事業を活用して専門家から長期的な視点のアドバイスをいただきたいです」(日野氏)
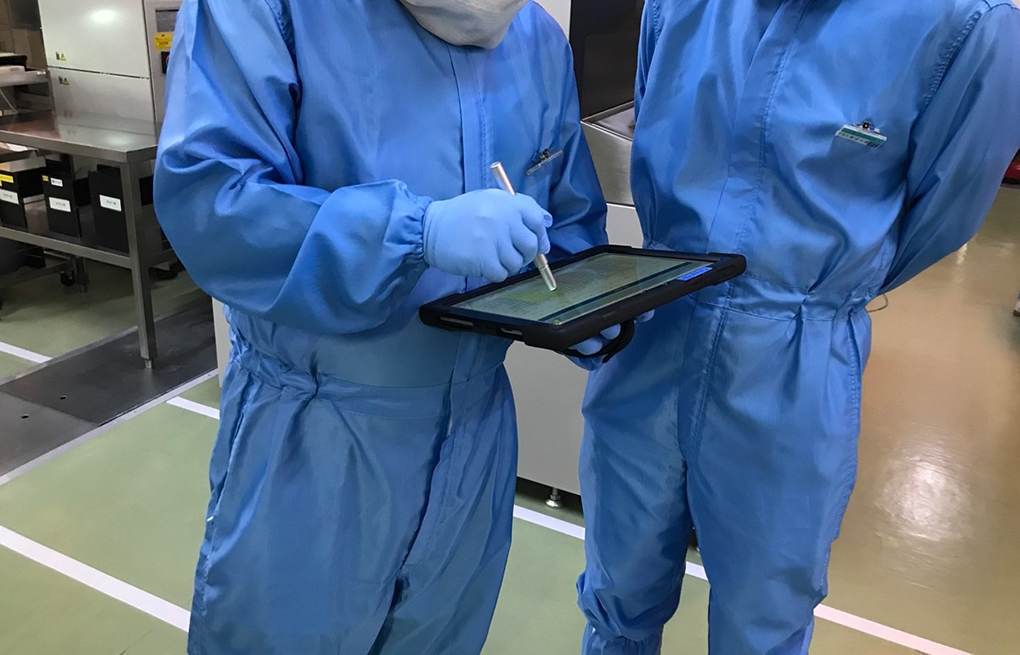
デジタル化と職人技の“共存”
〜モノづくりに集中してもらう環境の実現へ
IoTセンサーシステムと共に、「外観検査のAI化」の導入も並行して検討されており、取材時にはまだ社内での検証段階だった。「外観検査」とは製品の外観や状態を主に目視で検査することをいう。加工前後の製品に汚れ・傷・欠けなどが無いか品質管理のために行われる作業だ。同社の場合は、半導体などミクロメートル・ナノメートルの製品を扱うことになるため、外観検査には金属顕微鏡も用いられる。
「金属顕微鏡を覗くと気持ちが悪くなる人もいて、外観検査は誰でもできるものではありません。製造業全般は就職希望者が減ってどこも人手不足です。人が足りない分、検査の“みる”と“判断する”部分をAIに任せたいと考えました」(日野氏)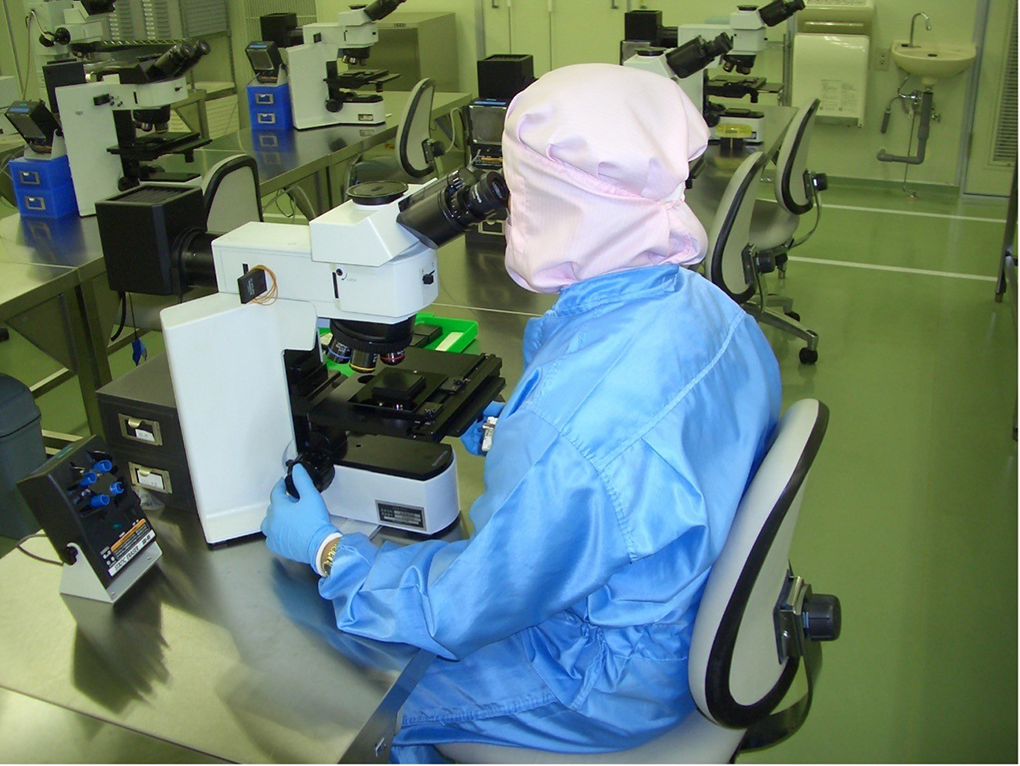
AI導入は人手不足への対応に加えて「取引先からの要求」も影響している。昔は不具合発生時の対応については企業同士の信頼で成り立っていたものが、近年は不具合が発生した箇所や履歴のデータ開示を求められることも増えている。取引先の高まる要求に人手だけでは対応するのが厳しい状況だ。
「最近のお客様はロボットや自動化されていることを重視する傾向にありますが、私たちの場合は逆で“人間にしかできないこと”に特化しています。イレギュラーなものや初めてのもの、最初のモノづくりは人間にしかできません。私たちがカタチにして、初めて量産となります。ロボットや自動化は同じ作業を繰り返す量産に必要なものです。私たちの求めるデジタル化は作業員の“モノづくりの職人”として能力を活かしてもらうための手段なのです。IoTセンサーシステムも外観検査のAI化も作業員がモノづくりに集中してもらう環境を実現させるデジタル化となります」(日野氏) 最後、日野氏にデジタル化を検討している中小企業へのアドバイスを伺った。 「まずは困っていること、社内の問題を整理することが大事です。そして今回派遣していただいたような専門家に相談して、何ができるのか提案をいただくことで方向性が見えてきます。同事業は助成金対象になるので費用面でも助かりました。中小企業がシステム導入するなら、自分たちに合うように変更できたり、サポートしてくれたりする会社を選ぶのがいいと思います」(日野氏)企業情報
- 社名
- 株式会社サンテック
- 所在地
- 東京都西多摩郡瑞穂町長岡2-1-10
- 設立
- 1997年
- 事業内容
- 半導体用シリコン・光学ガラスその他各種特殊素材のダイシング加工、研削・研磨加工
- 資本金
- 2,500万円
- 従業員数
- 48名