2019.02.14
樹脂成型機をIoTネットワークで繋ぎ、製品の製作プロセスを統合管理。
新規製品の導入も短時間で可能に!
株式会社富士製作所〈製造業〉
樹脂の射出成型は、溶かす、流す、固めるの各工程で様々な機能やカタチを実現する事が可能だ。特に近年は樹脂材料の多様化により、金属に近い物性やゴムの様な物性の樹脂材料を使える様になり、製品のバリエーションも格段に拡大している。従来、金属やゴムでしか実現できなかった製品も樹脂化する事で、より低コストでしかも軽い素材に変更可能となる。株式会社富士製作所は、創業57年を迎える射出成型の老舗企業だ。高齢化や後継者不足が問題視される下町の「もの造り企業」の中において、IoTネットワークを活用した最新の設備を導入。また自社の労働環境改善にも積極的に取り組むなど、大きな経営改革へと歩みだした。同社の代表取締役社長、望月氏に、IoTネットワークシステム導入のきっかけと、経営者としての想いを聞いた。
地元密着企業として生きる事を決意
富士製作所は、地元小松川を拠点に永年射出成型一筋に、数多くのプラスチック製品を製造する地元密着型企業だ。大手雑貨小売店の透明樹脂ケース、農機具の部品、クルマのキャリアの部品など、ここから生み出される製品は多岐にわたる。東京だけでなく商社を通じて日本全国から様々な樹脂製品の受注があるが、どんな製品でも対応できるノウハウは蓄積していると言う。同社では、下町の「もの造り企業」が抱える、ベテランの定年や後継者不足等の問題は無いのだろうか?創業から3代目となる望月氏に聞いた。
IoTネットワークシステム導入のきっかけ
望月氏:「実は、当社にベテランはもう居ないんです」と望月氏は言う。「実は、3年前程から新たな製品造りに対応する必要があり、当時の最新の成型機を導入しています。実は、既にこの時点で、当社の会長も高齢であり、最新の機械を扱えるのは私と若手従業員の数人しか居ませんでしたからね。」「この時点で意を決し、若い従業員を採用しました。現在の従業員の年齢構成は30代から40代と、同業の平均より遥かに若いと思います。ベテラン不在の中でしたが、機械自体も新しかったので、幸い従業員には一から教える機会が作れたのも結果としては良かったと思っています。」 業務の引継ぎは、比較的スムーズに移行し、特に障害は無かったという。その意味で同社は、同業の中小企業が直面する様々な危機を、既に3年前に乗り越えてきたと言えるだろう。これらの環境変化が次のステップである「生産機器のネットワークシステム」導入へと繋がる事になる。
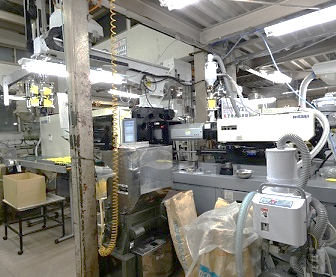
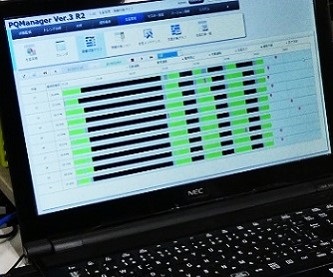
製品の製作過程を統合管理
同社は、「IoTネットワークによる成型機の統合管理システム」を2018年の9月から導入した。それ以前は紙ベースで管理をしていたという。新システムでは、成型機が稼動した過去の経緯が連続的に記録されるため、新しい品物を作り始める場合も、短時間で成型機のセッティングが可能になった。同社は、50トンから210トンの成型機を10台所有する。現在は成型機10台中8台がネットワークに繋がり、製品の製作過程を統合管理している。成型機稼働中の温度変化、スクリューの動き方、生産個数など、あらゆるデータを統合管理し、製作過程の記録が取れる仕組みだ。更に、異常を事前検知すれば成型機を止める。例えば、基準値を1とし、上下0.2以上変化すると警報を出し、異常値が3回連続すると自動停止する等の設定を、製品や成型機の特性によって決めておく事で、ほとんどのトラブルを防げるという。実際の導入効果を望月氏に聞いた。
今までできなかった事ができるようになり、生産の幅も広がる
望月氏:「現在は仕事の効率も大幅に上がっています。しかもグラフで生産経緯を確認できるので、生産工程を立てる仕事が楽になりました。また成型機に異常があった場合、従来は原因を突き止めるのに時間がかかりました。今は異常が数値で見えるので、例えば温度が変わった事が原因なのか、材料の入り方なのか等、どの異常値が出たら、機械を止めるように設定しておけば、大きなトラブルを防げます。従来、ベテランが経験上やってきた事が、きちんと理詰めで、従業員全体で共有できるのは、大きなメリットですね。当社は12月決算ですが、去年前年が1.8億、今年が2億、新システムの導入は、実際に売り上げにも反映しています。従来は生産の遅れで土日出勤もありましたが、今年はそれも無いですね。」
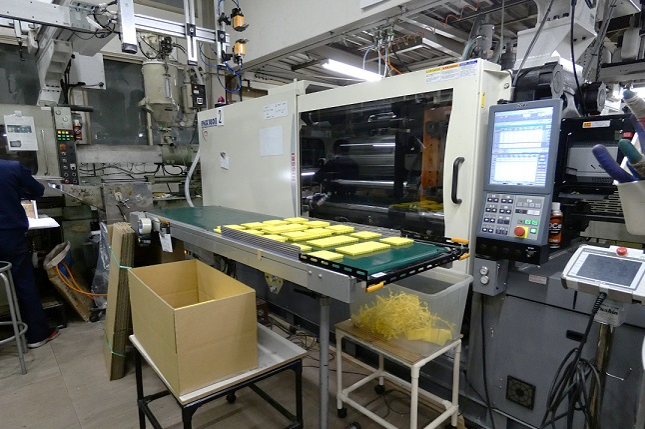
従業員の自信にも繋がっている
望月氏:「新たな製品を作り始める場合でも、たとえ難しい製品を受注しても、何とかなるという従業員の自信に繋がっていますね。導入後は今まであった不具合が無くなったと実感しています。実際の不良率はここ1~2ヶ月の間に大幅に下がっているし、作業効率は間違いなく向上しています。個々の機械の生産効率が上がることで、当然ながら工場全体の効率も上がり、工程計画も立てやすくなりました。」
成功の秘密は、新技術の導入だけではない
同社が、新システムを導入した事により、何かトラブルがあった時のリカバリーが早くなり、空いた時間で他の仕事ができるようになり、全体の効率は確実に上がっているという。近辺の工場は高齢化で辞めているところも多い中、同社は積極的に労働環境を改善し人材を確保している。周辺に住む主婦の方が多いので、朝9時から3時の間で週3回3時間のシフト等を作って働き方の多様化にも対応しているという。
労働環境の改善に注力。働きやすくするための、きめ細かい施策に着手
望月氏:「単純作業だし、細かい仕事ですから、働きやすい環境整備には結構気を使ったつもりです。例えば、8時間働く中で集中力が途切れて飽きてしまうんです。そこで3時間毎に休憩を挟んで違う仕事をしてもらっています。その方が飽きないし、ミスが少ないんです。面倒な作業を自動化したり、腰痛対策として作業者の椅子の高さを工夫したり、こんな工夫の積み重ねで、従業員も定着していきました。今は従業員のほとんどが日本人です。
interviewee
株式会社富士製作所〈製造業〉
取締役社長 望月 新史 氏
企業情報
- 社名
- 株式会社富士製作所〈製造業〉
- 所在地
- 東京都江戸川区小松川4-71
- 設立
- 1962年5月
- 事業内容
- 射出成型によるプラスチック製品製造
- 資本金
- 1000万円
- 従業員数
- 13名