2018.06.29
品質と生産効率アップの課題に向き合い
25年間地道な進化を続ける生産管理システム
石原金属化工株式会社〈製造業〉
「弊社のシステムは、社員の要望を汲んで複雑に進化し続けている。まるでガウディのサグラダ・ファミリアのようです」と語る石原金属化工(江戸川区)代表取締役社長の石原康裕氏。コストを抑えた自前のシステム構築をスタートして25年。「確かな品質」と「生産効率の向上」をモットーに、生産管理のIT化から稼働状況把握のためのIoT導入へと着実に歩みを進めている。
きっかけは作業の優先順位を整理しミス防止のために
石原金属化工は、従業員35名でコントロールケーブルおよび関連製品の組立を営む。
コントロールケーブルとは、フレキシブルリモートコントロールケーブル(Flexible Remote Control Cable)の略称。手元の操作による運動(力や運動)を、そのまま確実に遠方の離れた場所へ伝達させる遠隔操作の媒介の役目を担うワイヤーで、用途は自動車、船舶、建設、機械、住宅機器と幅広く、当社が扱う部品点数は約4,000点を超え、受注件数も毎月約1,000件、多品種小ロットの受注案件がその多くを占める。
手書きの指示書に頼っていた時代は、担当者が指示書を納期順に並べて作業をしていた。当時は、受注が月初にまとまっていて仕事量が把握しやすかったが、近年は、受注が週単位で小刻みになったうえに全体の受注件数も増加。案件の増加に比例して、生産現場での人的ミス、顧客からのクレームも増える傾向にあった。
これに危機感を覚えた石原氏は納期や優先順位を整理して、ミスを減らす対策を模索する。
1990年代、まだ製造業では注目し始められていた時期であったMicrosoft社のWindows3.1上にて稼働する表計算ソフトウェア「Excel」とデータベースソフトウェア「Access」にいち早く着目し、独学でマスター。業務に活用することで生産管理のデジタル化の第一歩を歩み始めた。
部品をデータベース化、指示書からスタート
年間50件のクレームを12件に削減
生産管理のIT化といっても、中小企業にとってコストは最大の課題。大手企業では、コストを投じ大手ITベンダーに依頼をすれば済む話であるが、同社にとっても選択肢は自前での構築以外になかった。
当時、国内ではまだ珍しかったMicrosoft Accessを独学でマスターした石原社長は、先ずは、地道に全ての部品に品番をつけ、発注先の社名・住所をデータベース化。そこに納期や注文残数を紐付け「製造指示書」を発行する最初のシステムを完成させる。
次に着手したのは「部品展開表」だ。同社は4,000点を超える部品の中から必要なものをピッキングして組立ラインに運んで作業を行う。最終製品の品目が7,000超パターンにも及ぶ組立業の同社にとっては、ピッキング作業の正確性の追求、効率化がミス撲滅にも直結する。様々な試行錯誤を繰り返し、オーダーに応じてピッキングすべき部品情報をシステム上で生成できるようにし、部品在庫数等とリンクすることで在庫管理も可能とした。
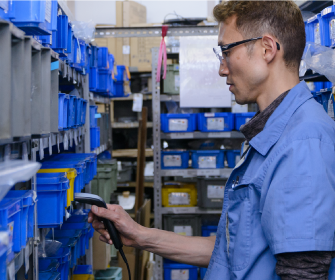
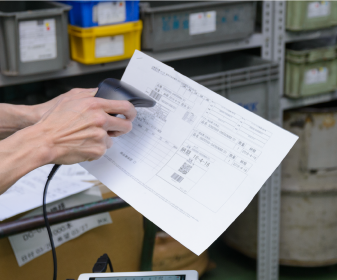
タブレットにバーコードリーダーを接続、これを設置したワゴンで部品を棚からピッキングする。部品展開表と棚のバーコードで取り違い防止が可能となった。
システム構築に長けた社員の入社を契機に、個別に稼働していた部品展開表をプログラミング言語(JavaScript)でリンクさせることで、現在の生産管理システムの土台を創り上げた。
また、導入とともに、現場作業を担う社員からもシステム自体の改善、携帯端末の導入要望等が上がるようになり、現在でも地道な改善が続く。
製造指示書では1シートで客先、部品名、部品の種類、製造の詳細、納品ラベルまでの情報が盛り込まれるようにしたり、端末入力自体が流れ作業にならないよう、作業員に確認を促す画面遷移や音声でのガイダンスが流れるようにするなど、細かな改善の積み重ねにより、人的ミスに起因する年間50件もあったクレームは、10件程度まで劇的に削減されることとなった。
全体の見える化でスムーズなコミュニケーションと品質向上を創出
生産管理のIT化はクレーム削減をもたらすだけで無く、全体の「見える化」と各部門の業務精度を向上させた。また、情報端末が廉価になったことも加わり、その管理に磨きをかけている。
製造残履歴や進行中の工程状況等を正確に把握することは、作業残の確認と業務の優先順位付けができるようになったことを意味し、スムーズな顧客への対応も可能にした。
更に2017年より、生産管理システムには、環境規制や製品要求の有無、過去のミスなどの注意喚起を受注案件ごとに書き込め、図面もアップロードして確認できる。チーム内でのノウハウを深め合うコミュニケーション機能は、導入早々品質向上に寄与している。
しかし、現在ではIT導入は一定レベルに浸透したが、導入当初や新機能の追加にあたり、社内の合意形成は、常に壁があることを石原社長は認める。
「社員の年齢層は幅広く、PC未経験者もいます。まず、就業時間以外はPCを自由に使えるようにしました。従業員が自由に使用できるWi-Fi環境も整備し、デバイスに慣れ親しんでもらう環境づくりに留意しています」(同氏)
「IoTの次はAI」実作業時間の把握、効率向上からその先へ
石原社長が次なるステップとして取り組むのは実作業時間の把握である。製造業では「価値を生み出す業務は、全体の三割程度」と言われ、製造機器の稼働率向上が利益向上につながる。
「まだ試験的な段階ですが、クランクプレス(プレス機械の一種)に加速度センサーを設置することで、いつ、何回機械が動いたかを割り出し、生産データを蓄積しています」(同氏)
データが積み上がると、各クランクプレスの使用頻度が明確になる。空いている機械に仕事を回せば、さらに生産性を上げられる。「データの蓄積と共に最終的にはAIを組み込み、生産の采配をAIで行うのが目標です」という石原社長。人口減少が目前に迫り人材不足が課題となる中、IoT・AIの導入で人的資源の効率化も視野に、次世代への安定成長を見据えている。
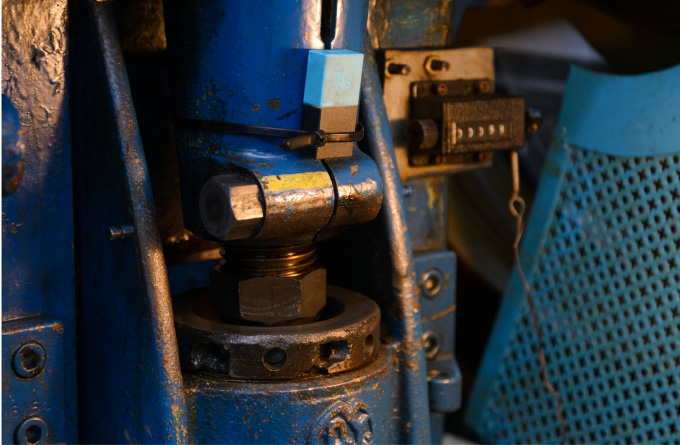
interviewee
石原金属化工株式会社〈製造業〉
代表取締役社長 石原 康裕 氏
企業情報
- 社名
- 石原金属化工株式会社〈製造業〉
- 所在地
- 東京都江戸川区平井7-6-10
- 設立
- 昭和29年8月17日
- 事業内容
- プッシュケーブル、プルケーブルの製造販売、 コントロールワイヤー、スピードメーターケーブル等の 製造販売・輸出、産業要素部品の輸入販売、油圧部品の販売など
- 資本金
- 1,800万円
- 従業員数
- 35名(2018年3月現在)